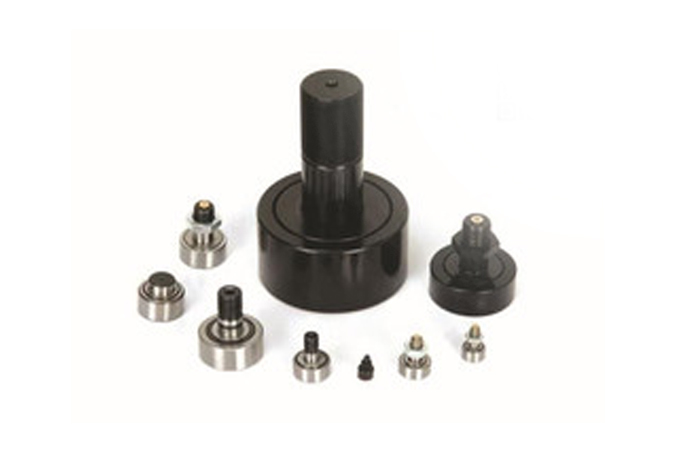
The outer ring of roller bearing adopts full cylindrical roller bearing with thick outer ring wall. The outer diameter surface of roller has cylindrical and arc shape, which can be designed to match with the raceway surface according to the application occasion. With this outer ring, the roller can roll directly on the raceway and can bear heavy load and impact load
The bearing is of sealed structure and filled with grease to provide long-term effective lubrication. Users can avoid lubrication. For those with bad working conditions, a channel for supplementing lubricating grease can be designed to improve the service life of the bearing. Improper method can also cause heating of roller bearing. Lubrication can reduce the wear of parts in motion, ensure the accuracy of press and reduce energy consumption. Lubrication is divided into thin oil lubrication and thick oil lubrication.
Composition of combined roller bearing
1) Main roller
The main roller is the main bearing body of a set of composite rollers, which mainly bears the load and impact load in the vertical direction, and has strong impact resistance, wear resistance and corrosion resistance. Since the main roller is a full loaded roller bearing, it can also be used alone as a one-way bearing.
2) Side roller
The side roller is the second bearing body of a set of composite rollers, which mainly bears the load in the horizontal direction, and also has strong impact resistance, wear resistance and corrosion resistance. The side roller is designed with no inner ring and full needle roller, and a mandrel is used to replace the inner ring and connect the bearing with the shaft head.
3) Shaft head
The shaft head is used as the connection part between the composite roller and the machine and equipment. Generally, the shaft head is designed as a chamfer for convenient installation. The shaft head can be directly welded on the equipment, or the shaft head can be welded on the connecting plate with round hole, and then the connecting plate and the equipment can be assembled.
4) Cover plate
The function of the cover plate is to fix the side roller installed inside the shaft head and the main roller outside the shaft head with nuts and thread glue at the tail of the shaft head.
Installation:
1) Wash the bearing with kerosene, press it into the bearing seat, fill the roller of the bearing outer ring with shell No. 3 lithium grease to two-thirds full, apply it evenly with clean hands, install the NTN bearing gland, and press the bearing gland with the fastening bolt coated with bolt locking glue;
2) The bearing is a cylindrical roller bearing with separable inner and outer sleeves. The bearing shall be sleeved on the rotating shaft and in place;
3) Install the bearing seat on the casing. If there is a grease filling hole, it must be aligned with the position. Tighten the bearing seat with the fastening bolt coated with bolt locking glue;
4) The inner and outer eccentric blocks are installed on the rotating shaft and in place. If there is a shaft key, install the shaft key into the keyway, then install the outer eccentric block, and install the shaft on the rotating shaft with a retaining ring;
5) Tighten the fastening bolts of the fixed eccentric block, rotate the adjustable eccentric block to reach the angular position before removal, and tighten the fastening bolts. After the above assembly, the rotating shaft shall have certain axial series movement;
6) Install the protective covers at both ends of the vibration motor and fasten them with screws.
Thin oil lubrication:
The advantage is that the internal friction coefficient is small, so it consumes less energy to overcome friction, has good fluidity of thin oil, is easy to enter the friction surface of each lubrication point, has good cooling effect, and can remove the impurities and impurities adhered to the friction surface. The disadvantage is that the oil film can not bear large unit pressure and has high requirements for sealing. High speed presses generally use large flow of thin oil lubrication, which can take away the heat generated by each friction pair.